Cocreating Sustainability
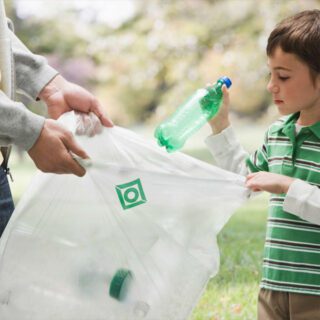
The Fifties:
The foundation for our current company was laid in 1948 by J.M. Oerlemans, who started with a contract spraying company. He soon discovered that trading in agricultural and horticultural supplies, including plastic film, was a logical extension of the first activity.
The Sixties:
A new plant with offices is put into service. The activities are expanded with so-called soil decontamination for greenhouse horticulture and open-field horticulture. The growth of the company necessitates another type of enterprise and gives cause for a new company name ‘Handelsonderneming Oerlemans NV’. In the next couple of years, the trade in film products and the soil decontamination are separated and incorporated in different companies.
The Seventies:
The activities regarding plastic film products are expanding. Partly due to the oil crisis, in 1973 a start is made with extruding plastic film. This is where a true production company arises.
The market segments of agriculture and horticulture, the wholesale of small packaging and the industry prove to have been the right choice. Indeed, the production capacity is rapidly becoming too small. New extruders and finishing machines are purchased, in order to meet the increased demand of the customers.
The Eighties:
Gradually, the number of producers and buyers increases. By now the pioneer stage, where a small assortment was manufactured with relatively simple means of production, appears to have been exchanged for a scale-up phase, where upscaling and modern means of production are indispensable. With the support of the then mother company Kleiberg Beheer BV , Oerlemans Plastics develops into a modern, advanced company. Oerlemans Plastics’ goal is to improve quality and expand its range of products. That is why they invest greatly in new premises during these years (by now 8000 m²) as well as in new machines, installations, and product development. The products of Oerlemans Plastics are sold in The Netherlands and the surrounding countries. In this period, the company has 70 employees.
The Nineties:
The investments in expansion towards the end of 1989 need to start contributing to the return by now. Quality awareness is introduced, in the broadest possible sense. The term ‘OPUS’ is launched, which is short for ‘Oerlemans Plastics Uit de Startblokken’ (= Oerlemans Plastics out of the Starting Blocks). This acronym stands for the necessity to increase the level of quality and service within the organization. By then, the premises comprise 10.500 m². The number of employees has risen to 100, and as of April 1st, 1990, the organization adheres to the NWBC CAO (Collective Labour Agreement).
The Year 1991:
Once again, a big step is taken towards expanding our company. The then mother company, Kleiberg Beheer BV, moves to an office building in the city of ‘s Hertogenbosch. The company is now able of fulfilling a long-standing wish: building a modern office building. By the end of 1992 the building is finished and the company has moved to the new premises.
The Year ’96/’97:
After several years of consolidation and optimization, it is time to expand the business further. By then, the business park in Genderen had become too small to realize all the plans for the future. New business premises are bought at Industrieweg 7 in Giessen. This object has an area of 20.000 m², of which 8.000 m² are built-up, and will house a print department and a finishing department. This enables the extrusion department in Genderen to expand further. A new film blowing technique is introduced. Previously, Oerlemans Plastics specialized in single layer extrusion. Now the customers can also buy multilayer products, the so-called coextrusion products. That was the year that Altas was taken over and integrated into the Giessen location. This takeover added loop-handled (DKT) carrier bags to the range of products. Now the company employs 105 professionals. Of these, 45 will work in the Giessen plant and around 60 people will work in Genderen.
The Years ’98/’99:
Oerlemans Plastics gradually grows even further. In these years, much money is invested in modernizing the machine pool in Genderen and Giessen. The workforce in both Genderen and Giessen has been expanded to 80 employees per location.
2007:
On May 31st, 2007, Kleiberg Beheer BV and CEO Joan Hanegraaf agree to transfer the shares of Oerlemans Packaging BV. This is a management buy-out. Joan Hanegraaf becomes the sole shareholder through Hanegraaf Holding BV. At that point Joan had been working for the Kleiberg Group for 22 years, since 1985, of which 13 years as a CEO. In the second half of 2007, the expanded print department is put into service. Once again, 500 m² of production space was added. This was necessary to find a place for the new investment: An 8-color W&H printing press. This new printing press is state-of-the-art in the field of flexoprinting, with a maximum output capacity of 600 m per minute. By the end of 2007, the largest part of the logistics department moves from Genderen to the new warehouse in Giessen. This expansion adds 4000 m² of floor space and 8000 pallet spaces. With the commissioning of this warehouse the long-standing, chronic shortage of storage space has finally come to an end, and we can focus on efficiently managing the internal and external logistic processes. At that point in time, Oerlemans Plastic employs 250 people, of which 85 work at the Genderen location and 165 are based in Giessen.
2019
In 2019, the machine pools of the Ecolon and Frisiapack companies are integrated in Oerlemans Plastics. The Oerlemans Technology Center (OTC) is opened in October, along with the startup of the Oerlemans Repro Center (ORC). Both business units add expertise to the product result of our partners; the OTC in the field of Research & Development and the ORC in the field of reprography and the monitoring of print quality.
2021/22
The Giessen plant of Oerlemans Plastics is expanded. By building a new, 25 m high extrusion hall, among other things, the built floor space of the company is doubled to 8.800 m².
2023
In this anniversary year (Oerlemans Plastics exists 50 years) the extrusion line-up in Giessen has been realized! With two ultramodern 7-layer extruders, a production line is set up of mostly recyclable packaging solutions that comply with current guidelines and contribute towards a process of a circular and environment-friendly economy.
At the end of the year, the office area in Giessen will be officially opened, coinciding with Oerlemans Plastics’ 50th anniversary. This was celebrated in style with colleagues and relations during the splashing Open Air Circular festival.
Oerlemans Plastics produces and supplies a full range of specialized, flexible films and packaging in paper and plastic variants. Oerlemans Plastics is part of the OPACKGROUP: seven manufacturers, ten production sites, independent research lab, inhome reprographics and more than 750 professionals with huge experience! We would like to unburden you; from design to packaging production and implementation.
In our digital product environment; innovation and sustainability meet in the diverse range of flexible custom packaging solutions. You can do this through our customised products or through the complete portfolio of the OPACKGROUP, of which we are part.
With a balanced mix of knowledge and passion for the packaging product, we specialize in developing advanced packaging solutions which not only meet but exceed the demands of today’s dynamic markets!
In our digital market environment, visitors have reached the destination for customized packaging solutions in a broad spectrum of sectors. We divide these into main areas food, non-food and agri/horticulture.
Discover the detailed market selections of our company and parent company OPACKGROUP, carefully tailored to specific industry needs. With a focus on customization and innovation, you will discover the perfect packaging solutions uniquely designed for your business.
Experience our expertise in packaging for different markets – your journey to customized solutions starts here!
Meet Oerlemans Plastics solutions: our online hub – dedicated to the unique properties of packaging. Discover innovative, sustainable customized solutions for a variety of industries. Consider flexible packaging options designed for ultimate product protection and environmental responsibility.
Help us shape a greener, more efficient future – together we can make IMPACT! A few examples:
Learn more about our latest developments, publications, blogs and articles with third parties in the Oerlemans Plastics newsroom.